ワイヤーハーネスの外観検査工程
2017年03月31日
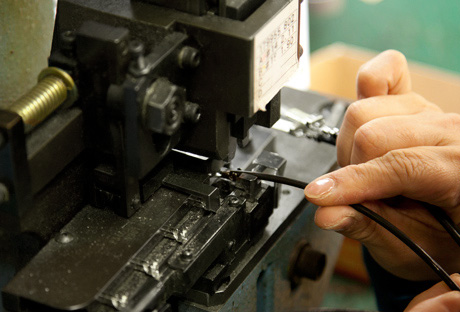
ワイヤーハーネスの製造における検査工程は導通検査、引張試験、外観検査工程に分類されます。外観検査工程ではワイヤーハーネスの寸法、部品、圧着・圧接・半田状態、汚れキズ、銘板などが正しいか目視によって検査します。
・寸法の検査
ワイヤーハーネスの全長や分岐部分、結束部分などの長さが指定された寸法と合致しているか検査します。検査は定規やメジャー、ノギスを用いて各部の長さを測定します。なお、寸法は公差内に収まっていれば合格です。公差とは基準値に対して許容される範囲のことで、例えば100mm±1mm(基準値±公差)のように表現されます。ワイヤーハーネスは短いと接続できないリスクが高まるため、マイナスの公差よりもプラスの公差の方が大きく指定されていることが多いです。
結束バンドがある場合は結束バンドの位置も計測し、正しい位置に適正な結束状態で結束されているか検査します。
・使用部材の検査
電線、ケーブル、コネクタ、端子、外装品など製作に実際使用されている部材が指定されている部材と合致しているか目視により確認します。形や色が似ているなどの要因で、間違った部材が使用されてしまう場合があります。正しい部材が使用されていれば合格です。
複数色の単線電線を使用しているワイヤーハーネスでは配線は正しく導通検査を合格するが、配色が間違っていて不合格となる場合があります。配色は目視でも確認できますが、カラーチェッカーと呼ばれる配色検査機も開発されています。
・コネクタ、ハウジングの挿入検査
コネクタ、ハウジングに端子が十分に挿入されているか検査します。コネクタ、ハウジング挿入作業で
挿入された端子は、挿入不足であると引っ張られると抜けてしまい接触不良の原因となります。電線を手で引っ張って端子が抜けなければ挿入が十分であると判断することができます。
・銘板の検査
各端末部や分岐部分に取り付けられている銘板の印字内容や文字サイズ、向き、色、形状、が正しいか検査します。銘板内容が間違っているとワイヤーハーネスの接続時やメンテナンス時に信号や接続の行き先を間違えるリスクがあります。
・圧着状態の検査
圧着状態を確認して電線の芯線部分と端子が正しく結線されているかどうか検査します。目視によって端子の曲がり、うねり、損傷、圧着不十分さなど端子形状から圧着状態が適切か確認します。芯線の状態からも圧着位置不良、浅打ち、深打ち、芯線漏れなど圧着状態の良し悪しが判断できます。またマイクロメータを用いてクリンプハイトと呼ばれる端子が電線の芯線をかしめている部分の高さを計り、クリンプハイトの値が適正値であるか定量的にも圧着状態を検査します。適正なクリンプハイト値は端子メーカによって規定されています。
・圧接状態の検査
圧接状態の目視検査では本体、プロテクタ、リリーフ・クランプ・カバー、電線の各種部品が浮きや空間がなく適正に圧接され装着されているか確認します。圧接状態が悪いと導通検査工程の導通試験、耐圧試験で不合格になる可能性が高いですが、目視でも圧接状態を確認します。
・半田状態の検査
半田状態を目視により検査します。半田状態は主に結線、半田量、表面、部品損傷を確認します。まず接合部品同士に半田がきれいに流れ込んでいるか(半田の濡れ状態)を確認します。次に半田の量が適正であるか確認します。半田の量が多いと意図せず周囲と通電してしまったり、逆にはんだの量が少ないとはんだが不十分で抜けや導通不良の原因となります。適正な半田は表面が滑らかです。半田の表面がざらついていると加熱過剰による合金の成長、フラックスの蒸発により半田が劣化し接合部の強度が弱く、導通も悪くなります。最後に半田による加熱過剰により部品や周囲が変形、変色、損傷していないか確認します。
・キズ、損傷、変形、変色、汚れなどの検査
ワイヤーハーネスに使用されている各部品のキズ、損傷、変形、変色、汚れなどの異常を目視によって検査します。より詳細な部分の目視をする場合は、拡大鏡やマイクロスコープを用いて検査します。微細な部分の検査には電子顕微鏡が使用される場合もあります。またコネクタカバー、ケーブルクランプ、端子台など部品組み立てにネジを使用する場合はねじ山が潰れて損傷していないか確認します。
・締め付けやロック状態の検査
ネジによる固定作業がある場合は、ネジにゆるみが無いか確認します。トルクが指定されている場合はトルクドライバーやトルクレンチで締め付けトルクを測定します。ネジや押し込みで固定するような部材がある場合は、しっかりと部材がロックされているか確認します。